A Comprehensive Guide to Welding Inspection Madison Specifications
Wiki Article
The Value of Thorough Welding Assessment in Industrial Applications
In the world of industrial applications, the relevance of precise welding examination can not be overstated. As we explore the diverse benefits of thorough welding examinations, one have to think about the wider implications on safety, integrity, and cost-effectiveness in commercial operations.Enhancing Structural Integrity
When it comes to welding assessment in commercial applications, boosting structural stability is paramount. The main goal of welding examination is to make certain that the welds are capable of birthing the expected loads and anxieties they will certainly run into in service.The relevance of maintaining structural honesty in bonded frameworks can not be overstated. Badly carried out welds can result in devastating failures, leading to costly repair work, downtime, and also endangerment of human lives. Inspectors play a crucial role in the lifecycle of industrial parts, supplying guarantee that the welding process provides the desired toughness and toughness.
Moreover, advanced technologies, such as phased array ultrasonic screening and electronic radiography, deal boosted abilities in identifying possible weaknesses, permitting restorative procedures prior to issues escalate. By prioritizing the honesty of welds via precise examination, industries can guarantee functional efficiency and extend the long life of their infrastructure.
Identifying Welding Defects
Recognizing welding problems is a vital element of guaranteeing the safety and reliability of welded structures. These issues can compromise the integrity of the entire assembly and, if left unaddressed, might cause catastrophic failures. Usual welding issues consist of porosity, fractures, incomplete blend, and undercutting. Each of these flaws occurs from particular reasons, such as incorrect welding methods, contamination, or inadequate warm control.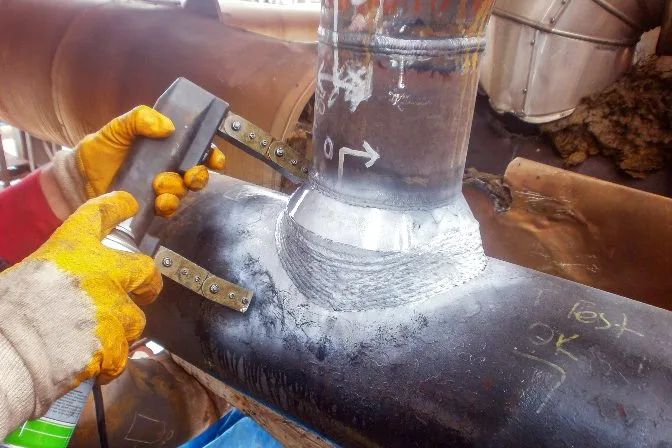
Competent inspectors use both visual examination and progressed non-destructive testing (NDT) approaches, such as ultrasonic or radiographic screening, to spot these defects. The prompt recognition and rectification of welding problems are important to maintain the architectural stability and durability of industrial parts.
Guaranteeing Compliance Specifications
Maintaining the honesty of bonded frameworks extends past identifying issues; it requires adherence to strict conformity requirements. Conformity with recognized standards, such as those offered by the American Welding Culture (AWS) and the International Company for Standardization (ISO), ensures that welds fulfill minimum security and quality demands. These requirements encompass a wide variety of standards, including product specifications, welding procedures, and qualification of welders. Adherence to these standards is essential to stop structural failures, which can lead to devastating repercussions in industrial applications.
Regular audits and assessments are crucial in confirming conformity. Examiners have to possess a thorough understanding of the relevant standards and be experienced at making use of various non-destructive testing (NDT) methods to review weld quality. By making certain that welding practices line up with conformity requirements, firms alleviate the threat of non-conformity, which can bring about legal responsibilities and safety and security risks.
Furthermore, keeping compliance not only safeguards structural stability yet also enhances a business's reputation in the sector. Stakeholders and customers are more likely to depend on companies that regularly demonstrate a commitment to top quality and security through extensive conformity. Thus, making sure compliance requirements is a critical part in the successful execution of welding in industrial applications.
Decreasing Maintenance Expenses
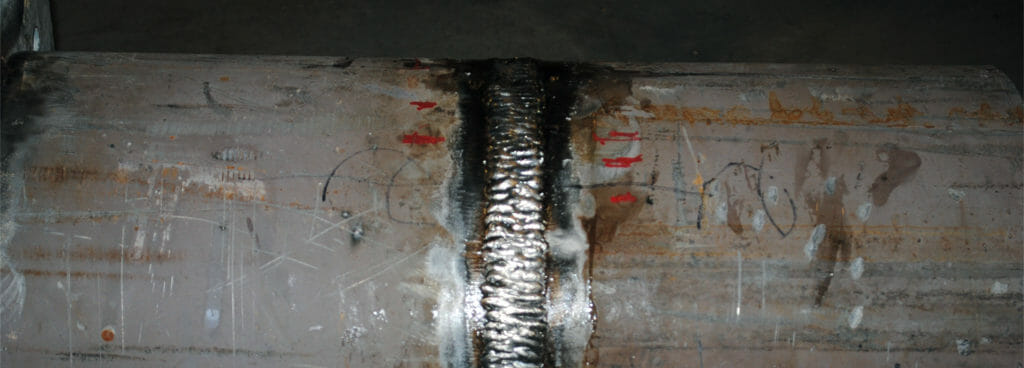
The application of advanced non-destructive testing (NDT) methods, consisting of ultrasonic, radiographic, and magnetic particle inspections, boosts the ability to discover subsurface defects without endangering the architectural integrity of elements. By employing these techniques, markets can dramatically extend the life span of their tools, lowering downtime and the Related Site connected monetary concern of upkeep tasks.
Moreover, a robust welding examination program sustains the optimization of maintenance schedules, shifting from reactive to anticipating maintenance approaches. This positive method not just reduces unexpected failings however additionally improves source allotment, making certain that upkeep efforts are concentrated and effective. Ultimately, the investment in strenuous welding assessment is balanced out by the considerable financial savings realized through reduced upkeep demands, contributing favorably to the total operational efficiency of commercial business.
Improving Precaution
Although safety is a vital issue in commercial procedures, accomplishing ideal safety criteria requires a devoted concentrate on the high quality and reliability of bonded structures. Welding assessment plays an essential role in this context, as it makes certain that all joints and links fulfill strict safety standards. Comprehensive inspections aid identify defects such as splits, porosity, or insufficient blend that can jeopardize structural honesty. Such issues, if left unaddressed, posture substantial dangers, potentially leading to catastrophic failings.To boost precaution, embracing sophisticated non-destructive screening (NDT) techniques is vital. Techniques like ultrasonic testing, radiographic testing, and magnetic particle assessment permit for thorough assessment without harming the structure. These modern technologies enable inspectors to discover covert imperfections early in the building and construction process, facilitating timely restorative activities. Additionally, carrying out a durable high quality control system that includes regular training for welders and assessors makes sure adherence to developed security standards.
Lastly, fostering a society of safety within the organization emphasizes the value of complete welding inspections. Urging open interaction and partnership among engineers, assessors, and welders adds to a common commitment to security excellence. Welding Inspection Madison. In doing so, industries can secure their procedures, shield workers, and keep public trust fund

Verdict
Detailed welding evaluation is crucial in industrial applications, dramatically enhancing architectural integrity and integrity. Eventually, the attentive execution of welding inspections plays a crucial function in keeping operational effectiveness and safety and security in industrial setups.As we discover the diverse advantages of persistent welding assessments, one must think about the more comprehensive implications on security, dependability, and cost-effectiveness in commercial operations.
The main objective of welding examination is to ensure that the welds are capable of birthing the anticipated lots and tensions they will certainly encounter in service. read Efficient welding assessment plays an important duty in minimizing these costs by guaranteeing the stability and durability of welds, consequently minimizing the danger of early failings.Extensive welding Get More Info inspection is indispensable in industrial applications, substantially improving structural honesty and reliability. Ultimately, the attentive execution of welding evaluations plays a crucial role in maintaining functional efficiency and safety and security in commercial setups.
Report this wiki page